Toyota 2008 Annual Report Download - page 35
Download and view the complete annual report
Please find page 35 of the 2008 Toyota annual report below. You can navigate through the pages in the report by either clicking on the pages listed below, or by using the keyword search tool below to find specific information within the annual report.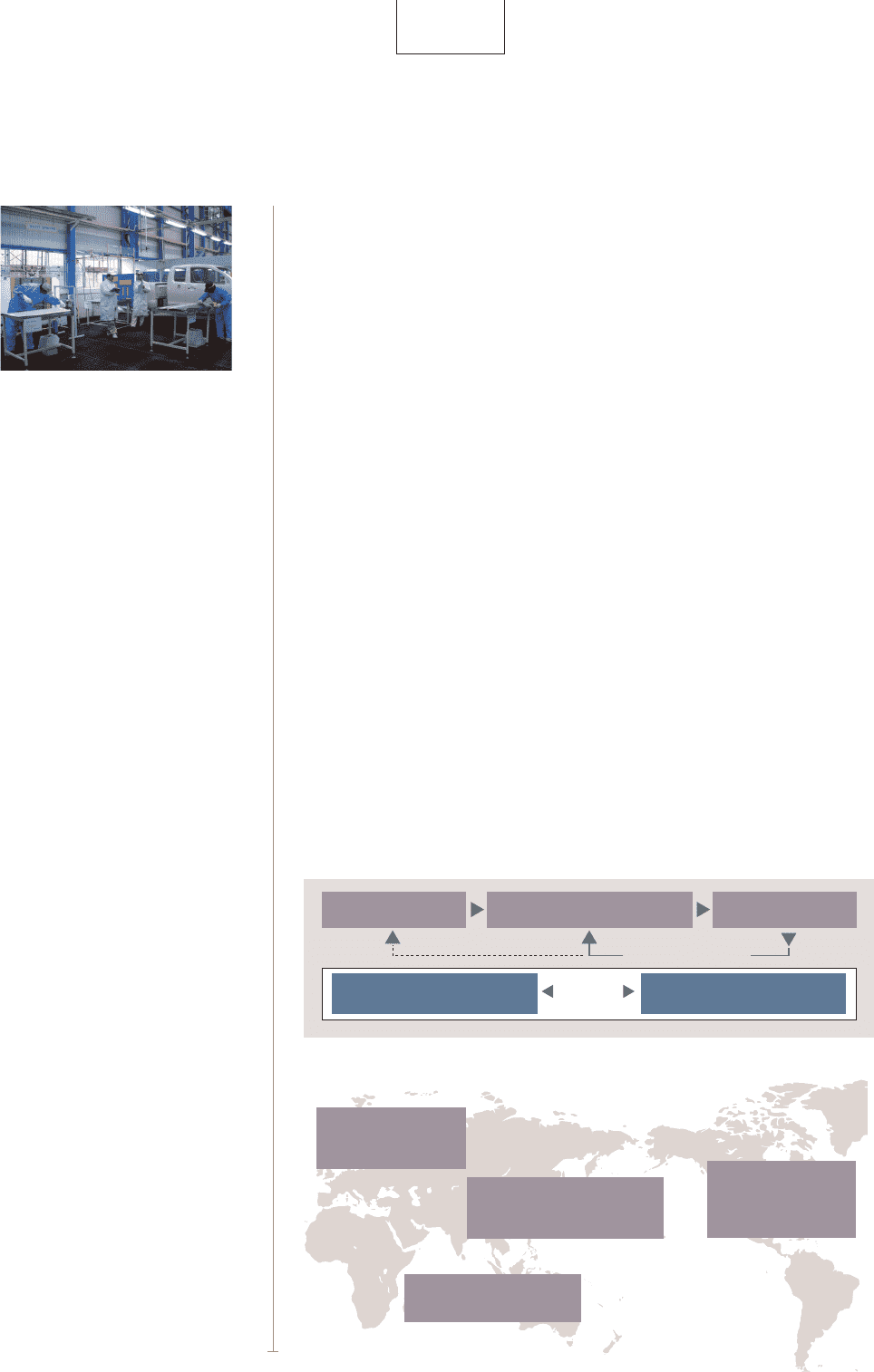
33
•Annual Report 2008 • TOYOTA
»Self-Reliance Supporting Programs
Historically, human resource development for Toyota’s overseas production
bases took place primarily at plants in Japan, using a “mother plant system.”
We found, however, that as the number of overseas manufacturing
companies grew, disparities in training content began to arise. So, in July
2003 we established a Global Production Center (GPC) at our Motomachi
plant in Japan. The goal of the GPC was to instill in employees the awareness
that all of our vehicles should offer the same “Made by Toyota“ quality
regardless of where in the world they are manufactured. At the GPC, skilled
technical personnel from plants in Japan teach the standard production
methods that form the Toyota production system. They use technical training
devices, animations, and other visual aids to enable overseas staff to quickly
acquire necessary skills. Between its founding in 2003 and May 2008,
approximately 13,000 workers underwent training at the GPC.
In 2006, overseas branches of the GPC were established in the United
States, the United Kingdom, and Thailand. This marked a transition from the
previous phase, in which Japanese trainers taught overseas personnel, to a
new phase in which local trainers pass on their skills to local personnel, as well
as personnel from other countries, to promote the spread of technical skills
on a global basis.
In addition, our three-year Pro-WIN* program for global human resources
development in production-related fields, such as production preparation,
production management, logistics, plant operation, and various other fields,
trains professional production staff to support greater self-reliance at overseas
manufacturing companies.
* Pro-WIN = Professional-Will Interact Needs
Performance Messages from the Management &
•Overview •Management •Special Feature •Business Overview •Corporate Information •Financial Section •Investor Information •
European GPC, U.K.
Established in 2006
19 trainers
800 trainees/year
Asia Pacific GPC, Thailand
Established in 2005
8 trainers
GPC in Motomachi Plant, Japan
Established in 2003
150 trainers
2,500 trainees/year
North American GPC,
Kentucky, U.S.
Established in 2006
14 trainers
300 trainees/year
Prepare a vision for
human resource development
Will: Achievement of clarification of
the professional skills by each employee
Needs: Achievement of clarification of the
professional skills which organization requires
Confirm individual development
situation / Design development plan
Move into action
Interaction
and
Balance
PDCA* (every year)
Flow of Pro-WIN Program
Global Expansion of the GPC
Technical training at GPC in Thailand
* PDCA = Plan, Do, Check, Action