Toyota 2014 Annual Report Download - page 18
Download and view the complete annual report
Please find page 18 of the 2014 Toyota annual report below. You can navigate through the pages in the report by either clicking on the pages listed below, or by using the keyword search tool below to find specific information within the annual report.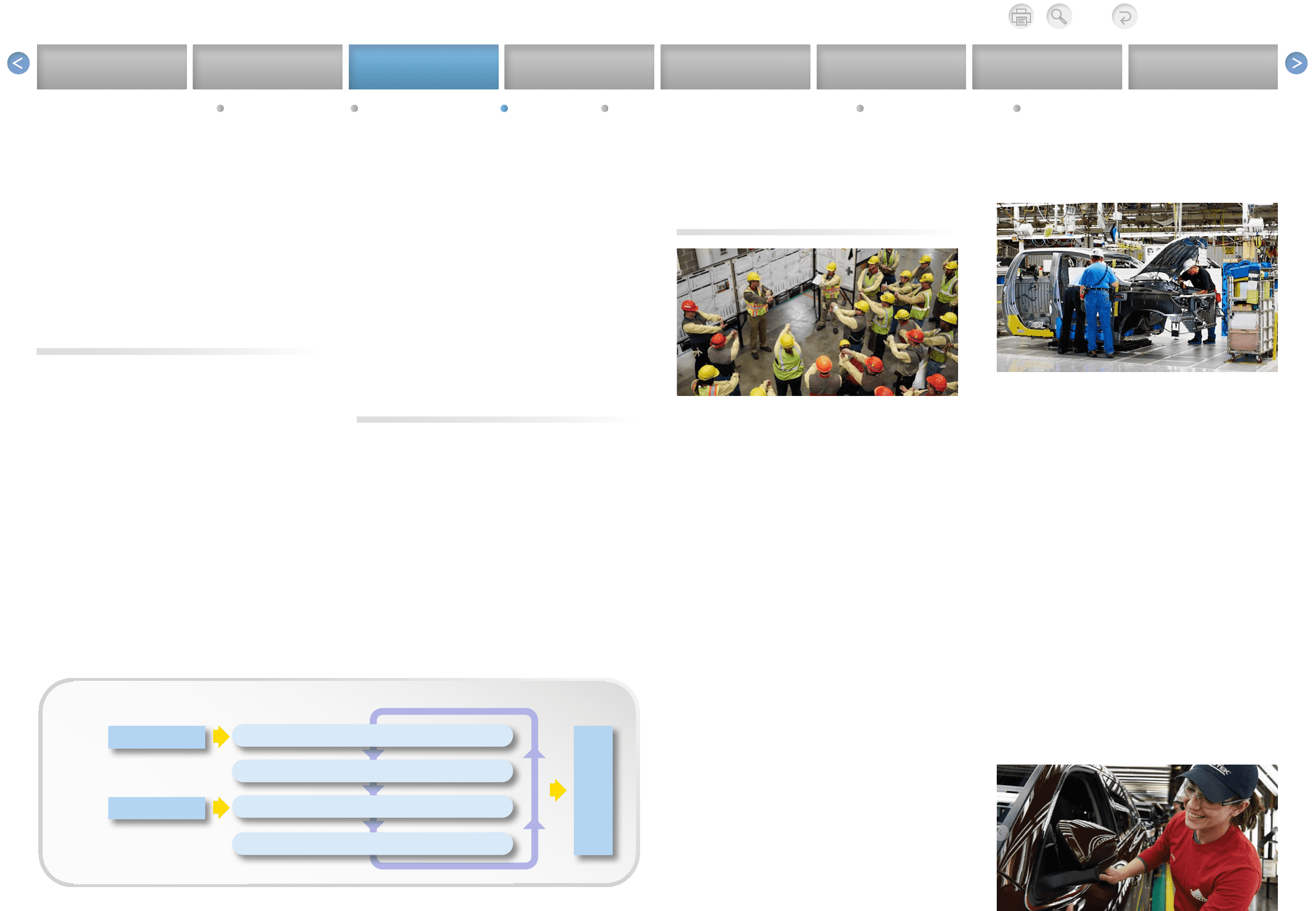
ANNUAL REPORT 2014
President’s MessagePresident’s Message
Overview of
Four Business Units
Overview of
Four Business Units
Special FeatureSpecial Feature
Review of OperationsReview of Operations
Consolidated Performance
Highlights
Consolidated Performance
Highlights
Management and
Corporate Information
Management and
Corporate Information
Investor InformationInvestor Information
Financial SectionFinancial Section
Page 18
NextPrev
ContentsSearchPrint
Toyota has grown from a single core concept
that is still shared by the entire Group: contrib-
uting to society by making ever-better cars.
Some of the values and ideas that have
defined Toyota over its 75-year history are
listed below.
The Toyota Production System (TPS)
TPS encourages the complete elimination of
waste, irregularities, and overburdening from
the production process. The system, originally
employed in the textile industry, is based on two
fundamental concepts: jidoka, which can be
loosely translated as “automation with a human
touch,” and the Just-in-Time (JIT) principle. Under
these concepts, if a problem occurs, the equip-
ment immediately stops running, preventing the
manufacture of defective products, and at each
stage production is limited to only what is needed,
when it is needed, and in the amount needed.
> Establish the facts through genchi genbutsu
(on-site, hands-on experience)
> Stop production lines when a problem
occurs and implement corrective and
improvement measures
Kaizen (continuous improvement)
Representing a never-ending cycle of progress, the
word kaizen encapsulates a spirit of striving for
continuous improvement and a refusal to accept the
idea that something cannot be made better. Toyota
believes that acknowledging the possibility of contin-
uous improvement can make tasks easier and more
enjoyable. From an organizational standpoint, kaizen
involves the entire workforce while relying on the
extensive knowledge, skills, and experience of the
people working directly on the process. The concept
is based on individuals taking ownership of their
work and focusing on what should be done rather
than on what can be done. At the same time, the
kaizen process is underpinned by thoroughgoing
and direct communication. It is essential to follow
through once a decision has been made upon
thorough deliberation with the participation of all.
We consider this a valuable part of our corporate
culture. Taiichi Ohno (1912-1990), a former Toyota
executive vice president and founder of the Toyota
Production System, once commented that while the
wisdom of humankind was infinite, that wisdom
tended to emerge only during periods of adversity.
When things are not going well and a better method
is discovered, it is critical that suggestions be made
openly, discussed, and put into practice to ensure
continuous improvement.
> The improvement process is infinite, and
after-the-fact improvements are in essence
forward-looking improvements
These directives, which form part of Toyota’s
management philosophy, are by no means limited
to the production front-line. They apply universally
to all endeavors. In effect, TPS represents the
building blocks of Toyota’s human resource
development endeavors.
Genchi Genbutsu
(on-site, hands-on experience)
The genchi genbutsu principle refers to much
more than merely visiting a site to examine some-
thing in situ. It entails understanding and respect-
fully considering the opinions of on-site individuals
as well as of individuals who have extensive rele-
vant knowledge. Genchi genbustu is thus a key
concept in the improvement process. Furthermore,
the notion of “respect for people” is consistent
with Toyota’s founding philosophy, and is under-
pinned by the concept of thoroughgoing and
direct communication.
Building “true competitiveness”
To consistently deliver a higher level of quality and
competitive products to its customers, Toyota
must continue to nurture a corporate culture that
places the utmost value on quality, productivity,
and cost efficiency. In addition to an unwavering
commitment to JIT that underscores our commit-
ment to the development of a short and efficient
supply chain, we realize that we must also
provide customers with a wide-ranging, compre-
hensive, and well-organized after-sales service
network. From a long-term perspective, we can
only stay competitive if we continue to focus on
developing human resources, fostering relation-
ships of trust between management and labor,
and ensuring that each employee remains
committed to conscientious manufacturing.
For its part, Toyota will continue to hone its true
competitiveness, which provides the underlying
strength for its manufacturing platform over the
medium to long term. By doing so, we hope to
ensure sustainable growth.
What Sets Toyota Apart
The Nature of the Toyota Production System
Take a close look at each site
Consistently uncover issues
Improve each issue
Raise management standards
Strengthen the Company’s
overall constitution /
Develop human resources
Kaizen (continuous
improvement)
The “Five Whys”
Toyota in 10 Years and 100 Years Our DNA is Creating Ever-Better Cars What Sets Toyota Apart Enriching Lives and Building Tomorrow’s Toyota through Innovation New Values for the Next Hundred Years Message from the Executive Vice President Responsible for Accounting