Toyota 2007 Annual Report Download - page 28
Download and view the complete annual report
Please find page 28 of the 2007 Toyota annual report below. You can navigate through the pages in the report by either clicking on the pages listed below, or by using the keyword search tool below to find specific information within the annual report.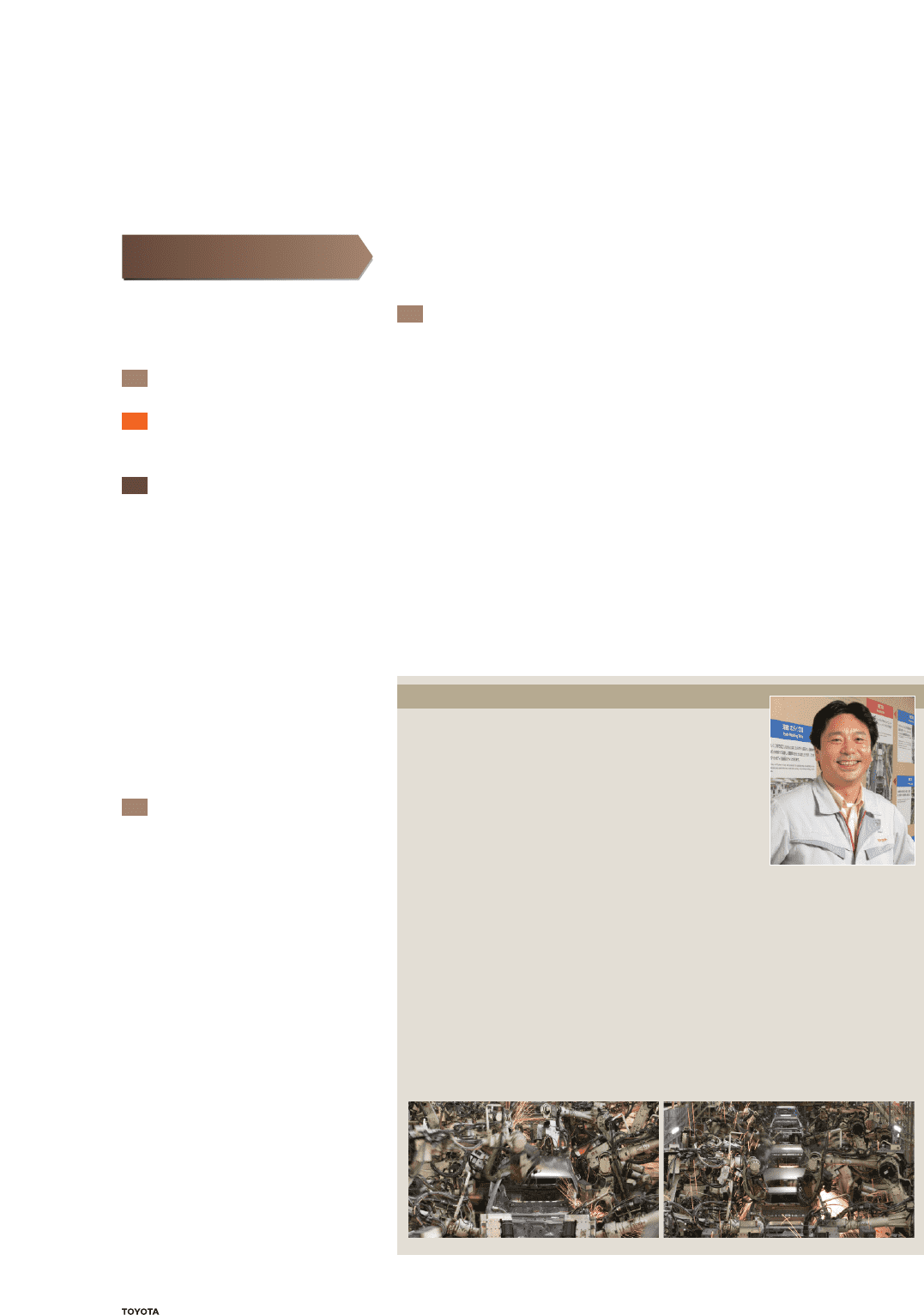
26 ANNUAL REPORT 2007
Innovating Next-Generation
Production Engineering Technologies
Innovation Challenges:
Toyota’s multifaceted production
engineering technologies innovation
has three main challenges:
Increasing the flexibility of pro-
duction lines,
Developing simple and stream-
lined production methods and
equipment, and
Ensuring high quality through
production processes.
Our production-related divisions
must tackle these perennial challenges
to maintain global competitiveness.
We must be able to adjust to chang-
ing production needs while constantly
setting new targets and working toward
them through production engineering
technologies innovation. Finding new
solutions is particularly important today,
with operations expanding rapidly
worldwide and a series of new manufac-
turing companies coming on stream.
Real Production Efficiency:
In theory, a production line continually
manufacturing a large volume of the
same model would achieve the high-
est production efficiency. However,
even though such a rigid production
line is very efficient when operating at
full capacity, if sales of the model
decline the line’s operating rate would
be down. And, it would not be easy to
change the production line over to
another model.
On the other hand, a single produc-
tion line with the flexibility to build
several models simultaneously improves
a plant’s ability to adapt to a range
of different production needs. Such
production lines make it easier to
adjust production plans to sales
trends. They also maintain high plant
capacity utilization because changing
or adding models requires minimal
time and labor.
Global Body Line Innovation:
Toyota has developed production
lines that can manufacture multiple
models more efficiently amid diversify-
ing demand and shortened delivery
times in the world’s automotive mar-
kets. The Global Body Line (GBL) is an
example of these efforts.
Toyota has been introducing its
groundbreaking body-welding line,
GBL, at plants in Japan and overseas
since 1996. As a result, GBL is now the
mainstay body-welding line in opera-
tions worldwide. Typically, between
4,000 and 5,000 spot welds and a vari-
ety of processes are needed to assemble
the body of a car from roughly 300
stamped parts. At this stage, accuracy
is critical. Because a car’s body is critical
to vehicle design, riding comfort, and
driving performance, welding process-
es must have assembly accuracy within
one millimeter of product drawings.
To achieve the required accuracy in
body assembly, devices called jigs
hold stamped parts in position to be
welded together. GBL significantly
improves production efficiency
through an innovative jig mechanism.
Not only that, GBL adapts easily to
large or small production volumes.
GBL’s predecessor, the Flexible Body
Line system, positioned jigs on the
outside of the car body and circulated
jig pallets. As a result, a production
Akitoshi Ichino
General Manager
Project Planning Department
Body Assembly Engineering
Division
Evolving GBL
In 1985, Toyota developed the Flexible Body Line (FBL),
which radically reduced jig replacement work arising from
model changeovers and allowed the mixed production of
four or five models. In 1996, pursuing a revolutionary new
concept, we developed the Global Body Line (GBL) that
added to the merits of FBL the ability to handle an even
more flexible mix of models. We introduced GBL in almost
all of our plants because it can adapt to a range of produc-
tion volumes—from high-volume production lines at plants
in Japan, North America, and Europe to low-volume pro-
duction lines at plants in such countries as Vietnam and the
Philippines.
The introduction of GBL has drastically increased the
efficiency of body-welding processes. Compared with FBL,
GBL has reduced costs for model changeover and addition
by 70% while cutting initial investment costs, floor space,
maintenance costs, and CO2emissions in half. In addition,
GBL can produce up to eight models simultaneously.
Aiming to further evolve GBL, we are developing a next-
generation body-welding line at our Takaoka plant.