Toyota 2007 Annual Report Download - page 30
Download and view the complete annual report
Please find page 30 of the 2007 Toyota annual report below. You can navigate through the pages in the report by either clicking on the pages listed below, or by using the keyword search tool below to find specific information within the annual report.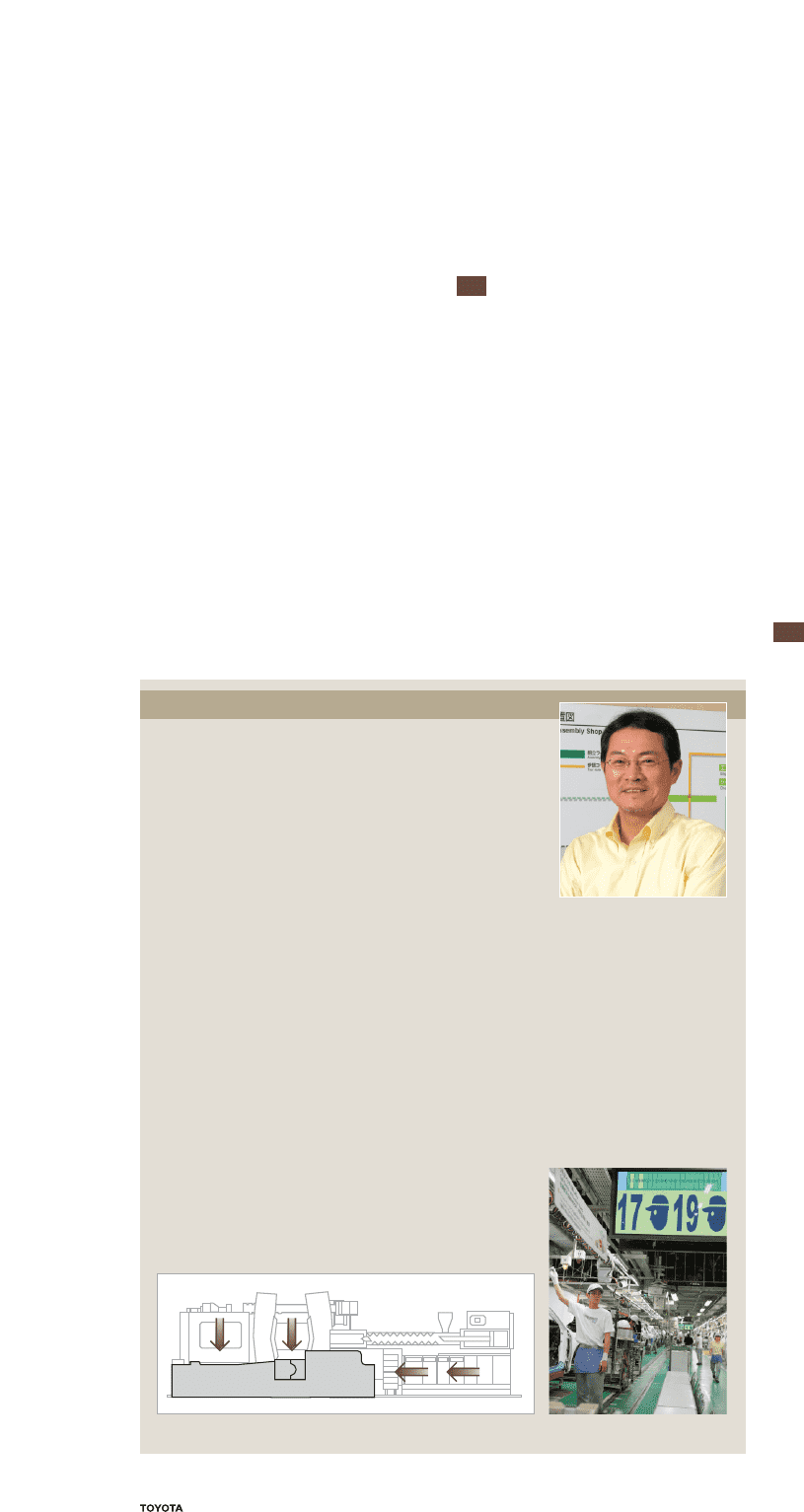
28 ANNUAL REPORT 2007
Clearly, such innovations in production
engineering technologies are realizing
enormous benefits. They not only
strengthen the competitiveness of
existing plants but also accelerate
Toyota’s global development by sig-
nificantly reducing the labor and cost
needed to start up new plants. Tradi-
tionally, it took nearly three months for
production lines at overseas plants to
become fully operational after start-
up. Now, it takes about three weeks. In
addition, initial costs for the construc-
tion of new plants have been cut
roughly in half.
Quality Assurance Systems:
Improving quality is a major focus of
our production-related divisions’ tech-
nology innovation efforts. Quality is
Toyota’s lifeline. The number one rea-
son customers choose Toyota vehicles is
for their high quality. We are moving
forward with strong efforts to maintain
product quality as the structure and per-
formance of vehicles become increas-
ingly complex and advanced and as
overseas production increases rapidly.
To ensure high quality, it is impor-
tant to examine designs meticulously
to develop manufacturing processes
and equipment that meet the required
quality standards. Accordingly, Toyota’s
production engineering experts are
involved from the early stages of
design and prototype development to
create designs that enable easy quality
assurance and manufacturing. Under
this system, the advice those experts
provide helps employees from various
production-related divisions understand
the quality standards they have to
meet and reflect them in production
processes and equipment.
Built-in Quality:
We have long believed in building
quality into products in the production
process. By this we mean that, rather
than inspectors ensuring quality, each
operator and piece of equipment
ensures quality so that defective prod-
ucts are never passed on to the next
process. Therefore, operators can stop
the production line to avoid forward-
ing defective products on to the next
process if they discover a defect or
something unusual. We are strict about
ensuring quality on the spot and then
sending the product to the next process
as opposed to making a lot of defec-
tive products and then repairing them.
A recent initiative is the stepped-up
introduction of in-line measurement.
This involves continuously measuring
the precision of products in respective
processes and controlling process
trends based on statistics derived from
the accumulated data. We can antici-
pate defective parts and always keep
production equipment in operating
status by monitoring product-preci-
sion trends that are approaching
threshold values. In addition to help-
ing us anticipate the occurrence of
defective parts, understanding trend
figures enables us to deal with single
items rather than lot units if a defect
arises. This initiative is a typical example
Current
Previous
Hisanori Nakamura
General Manager
Production Process Engineering
Innovation Division
Simpler, Streamlined Production Equipment
How far can production equipment be streamlined and
simplified? Toyota’s in-house development and innova-
tion of original production engineering is constantly test-
ing established ideas and preconceptions. For example,
our production robots can operate in small spaces that
people cannot get into, allowing us to drastically shorten
assembly lines. Changing over to robots has also enabled
the development of a conveyor system that is less than
one-tenth of the weight and length of the previous sys-
tem, which weighed tens of tons and was several dozen
meters long. In addition, we have fundamentally reviewed
the processes of such processing machines as stamping
machines, molding presses, and casting machines to cre-
ate significantly simplified and downsized equipment
that suits part sizes.
No longer limited to production engineering, streamlin-
ing and simplification are becoming a theme in the inno-
vation of production control systems. For example, we
are changing “Andon” from letters to graphic symbols.
Coupled with simpler, slimmer equipment, such innova-
tions enable anyone anywhere to use and maintain equip-
ment and systems—making a major contribution to our
current efforts to rapidly develop operations globally.
AndonDownsized injection molding machine for bumpers