APC 2006 Annual Report Download - page 28
Download and view the complete annual report
Please find page 28 of the 2006 APC annual report below. You can navigate through the pages in the report by either clicking on the pages listed below, or by using the keyword search tool below to find specific information within the annual report.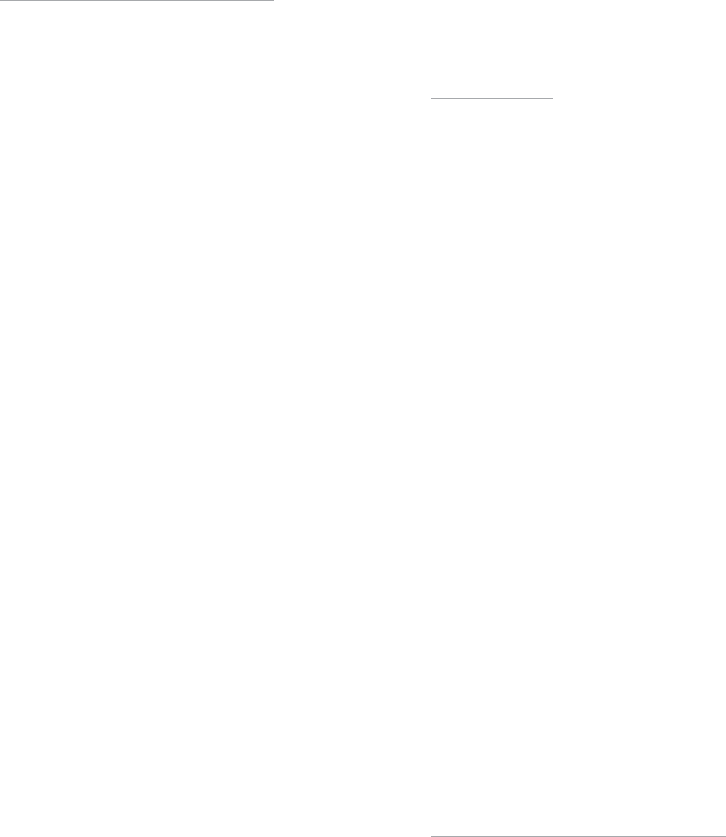
Schneider Electric primarily purchases raw materials
such as silver, copper, aluminum, steel and plastics, as
well as components, electronic products and services.
The supplier list includes international firms, as well as
many medium sized companies.
Suppliers are selected for their know-how, the quality
of their products and services, their competitiveness
and their compliance with environmental and human
rights requirements. Schneider Electric supports the
United Nations’ Global Compact and encourages its
suppliers to join as well. A sustainable development
agreement sets out each party’s specific commit-
ments.
Worldwide redeployment
of production and supply chain
resources
Schneider Electric has more than 200 production sites,
of which 45% manufacture for the global market. The
other units are located as close as possible to their end
markets. Although design or esthetic features may be
adapted to meet local requirements, the Group stan-
dardizes key components as much as possible to max-
imize economies of scale. This global/local approach
helps Schneider Electric optimize profitability.
Drawing on its global scope, the Group intends to build
lasting competitive advantage to support long-term,
profitable growth. A large number of projects have
been initiated around the world to re-balance and opti-
mize manufacturing and supply chain resources. The
Group’s objectives are to:
Produce as close to customers as possible to improve
service quality and responsiveness.
Achieve a lasting balance between production costs
and revenue within each currency zone to limit the
impact of foreign exchange fluctuations.
Produce and source in the most competitive region
for a given product. This means low-wage countries for
products with a high labor content, for example, and
developed countries for complex, highly automated
processes and services that require a strong local
presence.
In Western Europe and the United States, rightsizing
plans have been deployed with a focus on specializing
units, reducing their number and increasing their size.
At the same time, the Group has moved manufacturing
closer to demand by increasing capacity in Eastern
Europe, Mexico, India, China and the rest of Asia.
An industrial excellence program called Schneider
Production System has been deployed in all plants to
substantially and continuously improve quality, service
and productivity. Based on a Lean Manufacturing
approach, SPS is supported by the extension of Six
Sigma and Quality and Value Analysis programs
across the Group. By deploying these optimization
methods globally and sharing best practices, the
Group intends to lift the operational performance of all
its plants to the same high standard.
Schneider Electric’s plants and products comply with
increasingly extensive and stringent environmental
laws and regulations in all host countries, often antici-
pating new legislation when appropriate. Plants and
products also comply with international standards gov-
erning environmental protection in all host countries.
In order to limit risks related to the environment gener-
ally, the Group has implemented an ISO 14001-com-
pliant process to continuously improve the environ-
mental performance of its plants and logistics centers,
along with an eco-design process for products.
In 1992, Schneider Electric defined a formal environ-
mental policy, which was revised in 2004 to take
account of changes both inside and outside the Group.
This policy is designed to improve production process-
es, promote eco-design, integrate customer expecta-
tions into the Group’s environmental protection
approach and raise awareness among all employees
and partners about environmental protection and ener-
gy savings.
A major IT
systems project
On November 2, 2004, Schneider Electric signed a
contract with Capgemini with the goal of enhancing
efficiency and reducing the IT function’s overall cost.
The two-pronged contract involves outsourcing all of
the Group’s IT functions and departments in Europe
and designing, developing and deploying a global
SAP-based ERP system called Bridge that will be
installed in all units. The IT departments of some 100
European subsidiaries in 31 countries were effectively
outsourced in 2005.
Bridge’s design phase was completed at the end of
2006 and construction is scheduled for the first quarter
of 2007. The system will be deployed at several pilot
sites from 2007 to 2009. Bridge will then be installed
throughout the Group over a period of four years.
A dedicated governance and cost-control organization
has been set up to monitor the challenges and reduce
the risks involved in this project.
8. Human Resources
Developing a global system
for managing human resources
The human resources function’s missions are to sup-
port growth, prepare the future, develop competencies,
anticipate changes in the Group’s businesses and cre-
ate an attractive and stimulating work environment. At
the corporate level, human resources management
policies focus on training, compensation, international
mobility and workplace health and safety. These poli-
cies provide general guidelines that are applied
through local programs.
Description of the company and its businesses
26