APC 2006 Annual Report Download - page 90
Download and view the complete annual report
Please find page 90 of the 2006 APC annual report below. You can navigate through the pages in the report by either clicking on the pages listed below, or by using the keyword search tool below to find specific information within the annual report.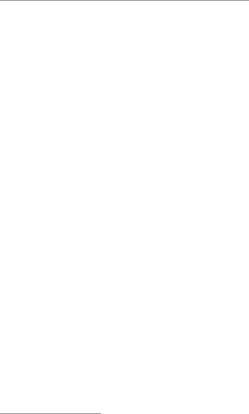
Business review
Promoting renewable energy sources
The Group is also making wider use of renewable
energy sources. For example, the corporate restaurant
at the Electropole R&D Center in Eybens, France is
powered by solar energy.
The International and Iberian Operating Division’s new
headquarters is equipped with a photovoltaic system
and a centralized HVAC solution that reduces energy
costs by 15%. And the Group’s future headquarters
under construction in Rueil-Malmaison will comply with
France’s HQE green building standards, notably as
concerns energy consumption.
Respecting ecosystems
Schneider Electric’s plants in Seneca and Columbia,
South Carolina have introduced innovative initiatives to
help protect wildlife on their sites. Thanks to time vol-
unteered by employees, the plants created or re-creat-
ed native wildlife and plant habitats in partnership with
community groups through the Wildlife and Industry
Together (WAIT) program.
Projects included a Carolina Fence garden, butterfly
and shade gardens, bluebird boxes and amphibian
houses.
Employees and partners have made recommenda-
tions for future activities to make wildlife preservation
an integral part of property and production area man-
agement.
Releases,
nuisance and waste
Land use
Virtually all Schneider Electric sites are located in
urban or industrial areas and do not affect any notable
biotopes. None of the Group’s businesses involve
extraction or landfarming.
Releases into the water and air
Because Schneider Electric is mainly an assembler, its
releases into the air and water are very limited.
Mechanical component production workshops are
carefully monitored, in keeping with their ISO 14001
certification. Their releases are tracked locally as
required by current legislation. No major spills or
releases were reported in 2006.
The Group’s actions are guided by the principle of
continuous improvement. In 2005, for example, the
Beaumont-le-Roger plant stopped using trichloroeth-
ylene as a cleaning solvent, while in 2006, Rectiphase
in France phased out zinc metal spraying for its
capacitors.
Special attention is being paid to volatile organic com-
pound (VOC) emissions in accordance with the so-
called best available technology (BAT) directive
(96/61). These emissions are covered by a compre-
hensive reporting system deployed in 2005.
For medium voltage products and equipment, the
Group has signed a voluntary agreement to eliminate
SF6 emissions throughout the devices’ life cycle. This
entails producing and operating in leak-proof condi-
tions and offering an end-of-life recycling service.
Releases into the soil
No substances are purposely released into the soil in
the course of site operation. Workshop flooring is spe-
cially treated to prevent any leakage. Hazardous sub-
stances are systematically stored and handled in
areas equipped with retention tanks. Retention sys-
tems are designed to compensate in the event of mal-
functions or emergencies, such as fires.
During the year, Schneider Electric conducted its
annual review of pollution risks at all manufacturing
sites as part of ISO 14001 tracking.
None of the sites are classified Seveso. However, the
Group continuously monitors 13 facilities, of which 7 in
France, often because of their past manufacturing his-
tory. Monitoring is conducted in liaison with local
authorities and preventive measures are carried out
when necessary. Such measures were taken at the
Yates site in the United States and at Maizières-les-
Metz in France, where soil contaminated by trans-
former oil was excavated. No major incidents were
reported in 2006.
Noise and odors
All Schneider Electric sites comply with noise limits.
Waste
Waste represents the majority of the Group’s releases.
Waste management is continuously being improved,
with a recovery rate of more than 80%.
Because classification systems vary widely from coun-
try to country, the Group does not consolidate global
data by category (hazardous and non-hazardous).
Waste is processed to ensure local traceability. In
France, for example, hazardous industrial waste
accounts for around 14% of total waste. All waste is
channeled to the appropriate treatment facility.
End-of-life management
The Group informs customers about its products’ envi-
ronmental impact and provides Product Environmental
Profiles (PEPs) to assist them with disassembly.
In Europe, Schneider Electric offers a service to take
back end-of-life products.
In 2006, MGE UPS Systems launched the “Swap pac”
program so that customers would not have to manage
electrical and electronic waste from outdated uninter-
ruptible power supplies. The program comprises an
environmental review of the installation’s electricity
consumption and quality; removal and certified
destruction of the end-of-life equipment; and delivery
of new equipment.
This goes far beyond the requirements of waste from
electrical and electronic equipment (WEEE) regula-
tions, which concern only a very small portion of
Schneider Electric’s lineup.
88