Toyota 2012 Annual Report Download - page 14
Download and view the complete annual report
Please find page 14 of the 2012 Toyota annual report below. You can navigate through the pages in the report by either clicking on the pages listed below, or by using the keyword search tool below to find specific information within the annual report.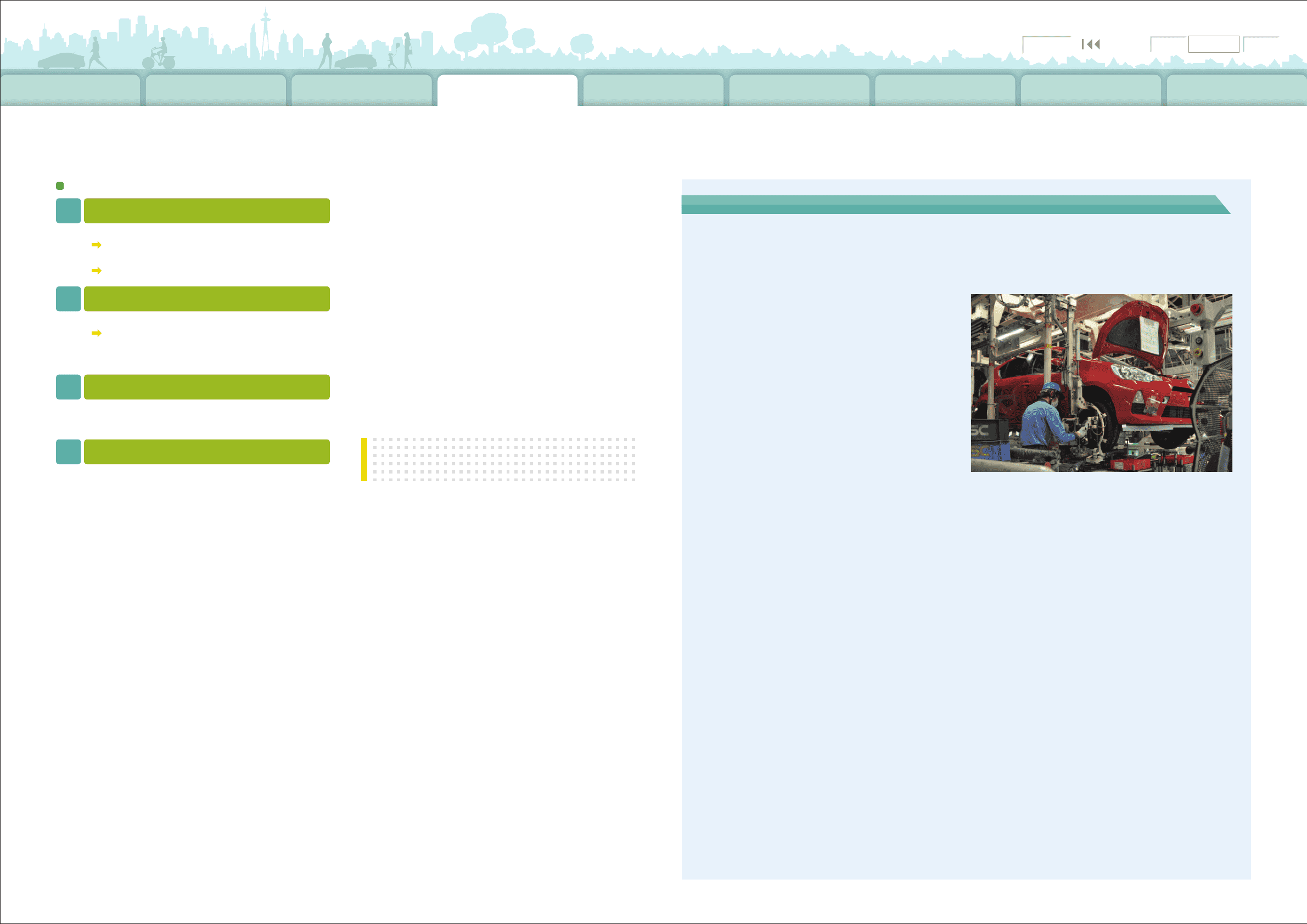
Management and
Corporate Information Investor Information
Changes for Making
Ever-Better Cars
Toyota Global Vision Business and
Performance Review Financial Section Special FeaturePresident
ʼ
s Message Medium- to Long-Term
Growth Initiatives
TOYOTA ANNUAL REPORT 2012
The Aqua and New Corolla, Featuring
World-Class Fuel Economy*
-
Making Tohoku the compact
monozukuri
base.
Integrating Production in
Tohoku and Building a Trilateral
Domestic Production Structure
Kanto Auto Works, Central Motor Co. and Toyota
Motor Tohoku Corporation merged
(
as of July
1, 2012
)
; creating Toyota Motor East Japan,
Inc.
(
TMEJ
)
. Tohoku will be our third vehicle
manufacturing hub in Japan after the Chubu and
Kyushu regions. We aim through this integration
to establish a comprehensive automobile
manufacturer that plans, develops and produces
compact cars and also manufactures components
and supports overseas Toyota operations.
Under the trilateral system, Chubu will be the
core of domestic production and the development
hub for new technology and new manufacturing
methods. Kyushu will be the hub for mid-sized
and Lexus brand vehicle production, and Tohoku
will specialize in compact cars.
We believe that establishing the technologies
for specialized mass production of certain vehicle
models by each regional company will accelerate
the advance of Japanese
monozukuri
, and to
that purpose we will maintain a 3 million vehicle
production capacity in Japan. We will reach a new
level of international competitiveness by creating
an environment for producing innovation through
the interaction of the technology development
and product planning units with the frontline
production and sales units. This will strengthen
the autonomy of each hub as well as the trilateral
system itself.
Toyota put our 17 years of mass-produced HV
development know-how and experience into making
components such as the compact, light, efficient HV
system that powers the Aqua, which is top in its class
worldwide in fuel economy.* Toyota is producing an
entirely new class of compact hybrid. We also have
launched a new version of our popular Corolla, a
compact car that is perfect for Japanese roads and our
customers, and for which global sales have reached
39 million units.
The Aqua went into production at the Kanto Auto
Works
(
currently Toyota Motor East Japan
)
Iwate plant,
while the Central Motor Co.
(
also currently Toyota
Motor East Japan
)
Miyagi plant was chosen to produce
the new Corolla. Both plants are in Tohoku, and the
selection of these plants marks an important step
toward improving manufacturing competitiveness in
Tohoku. Toyota wants to be a force for the revitalization
of Japan, and we are moving forward with
monozukuri
that has strong regional roots.
*As of July 2012
Production Topics
“Simple and slim” means durable equipment that is easy
to repair and is kept as simple as possible. This leads
to less capital investment and minimizes depreciation.
A real-world example of this simplication by going
from a 2:1 to a 10:1 volume ratio for press, casting and
forging molds. Other equipment and lines are also
slimmed down and simplied as much as possible, right
down to the plant building itself.
“Variable models in variable volume” means taking
a exible approach to model and volume changes. This
requires a scalable-length nal assembly processing
line, as well as engine and transmission lines that enable
simple equipment changeovers.
“Net shaping” means bringing the shape of the
product, especially at the post-rough-shape processing
stage, closer to the nal shape. A real-world example
of this is the application of craftsmanship know-how to
automation equipment to achieve reduction in material
loss rates from 80% to 90%.
“High added value” means more compact, higher-
performance, and more affordable components,
including hybrids, and the development of production
technologies that enable the making of high-
performance cars.
This innovation requires the digitization and quan-
tication of the experience and craftsmanship that have
been passed down, and the adoption of it in innovative
technologies. Then, further honing these skills and
techniques and adopting them in innovative technolo-
gies leads to greater innovation, producing a virtuous
cycle of craftsmanship-skill and innovative technology.
Keywords for Technological Innovation
Simple and slim
1
- Simple equipment
Break-resistant, easy to repair
- Capital investment reduction
Depreciation cost reduction
Variable models in variable volume
2
- High-volume production line
Small-scale production line
(
Eliminate waste of production capacity
)
- Simple set-up changeovers to new/different models
High added value
4
- More compact, higher performance, more stylish,
more reasonably priced
Net shaping
(
of the TPS 7
muda
, helps eliminate
waste from over-processing
)
3
- Process reduction
(
reduce stock removal
)
- Craftsmanship
The Toyota Production System as well as the new
technology and product development and production
that support it were created in Japan. The advanced
technologies created through the joint efforts of our
strong Japanese production centers and our suppliers,
and the high-value-added
monozukuri
represented
by the development of our hybrids will remain in
Japan, where it is important that we continue to hone
monozukuri
. When Toyota rst achieved output of 3
million vehicles in 1980, our output outside Japan was
a mere 200 thousand, but it has since increased greatly,
reaching our current level of 5 million cars produced
overseas. The foundation that has enabled that
achievement is our domestic production structure of 3
million units. Toyota will maintain this 3 million domestic
production structure, maximizing the competitive
superiority of high-tech Japanese
monozukuri.
Quickly
spreading the innovative technologies developed
and nurtured in Japan will in turn improve Toyota’s
competitive advantage outside Japan.
Domestic Output of 3 Million Vehicles
—
For Competitive Strength
Search NextPrev page 14
Contents
0821